The Ultimate Guide To Alcast Company
The Ultimate Guide To Alcast Company
Blog Article
Indicators on Alcast Company You Need To Know
Table of ContentsThe Alcast Company StatementsEverything about Alcast CompanyOur Alcast Company PDFsSome Ideas on Alcast Company You Should KnowThe smart Trick of Alcast Company That Nobody is DiscussingThe smart Trick of Alcast Company That Nobody is Discussing
Chemical Comparison of Cast Aluminum Alloys Silicon promotes castability by lowering the alloy's melting temperature level and improving fluidness throughout casting. Additionally, silicon adds to the alloy's strength and use resistance, making it valuable in applications where longevity is essential, such as vehicle parts and engine parts.It also boosts the machinability of the alloy, making it easier to refine right into finished products. In this method, iron adds to the general workability of aluminum alloys. Copper enhances electric conductivity, making it advantageous in electric applications. It also boosts rust resistance and contributes to the alloy's total toughness.
Manganese adds to the stamina of aluminum alloys and enhances workability (Casting Foundry). It is generally used in wrought aluminum items like sheets, extrusions, and accounts. The presence of manganese aids in the alloy's formability and resistance to cracking throughout manufacture procedures. Magnesium is a lightweight element that offers strength and effect resistance to aluminum alloys.
The smart Trick of Alcast Company That Nobody is Discussing
It permits the manufacturing of lightweight parts with excellent mechanical properties. Zinc enhances the castability of aluminum alloys and assists regulate the solidification procedure during casting. It enhances the alloy's strength and hardness. It is often found in applications where complex forms and great details are needed, such as ornamental spreadings and particular vehicle parts.
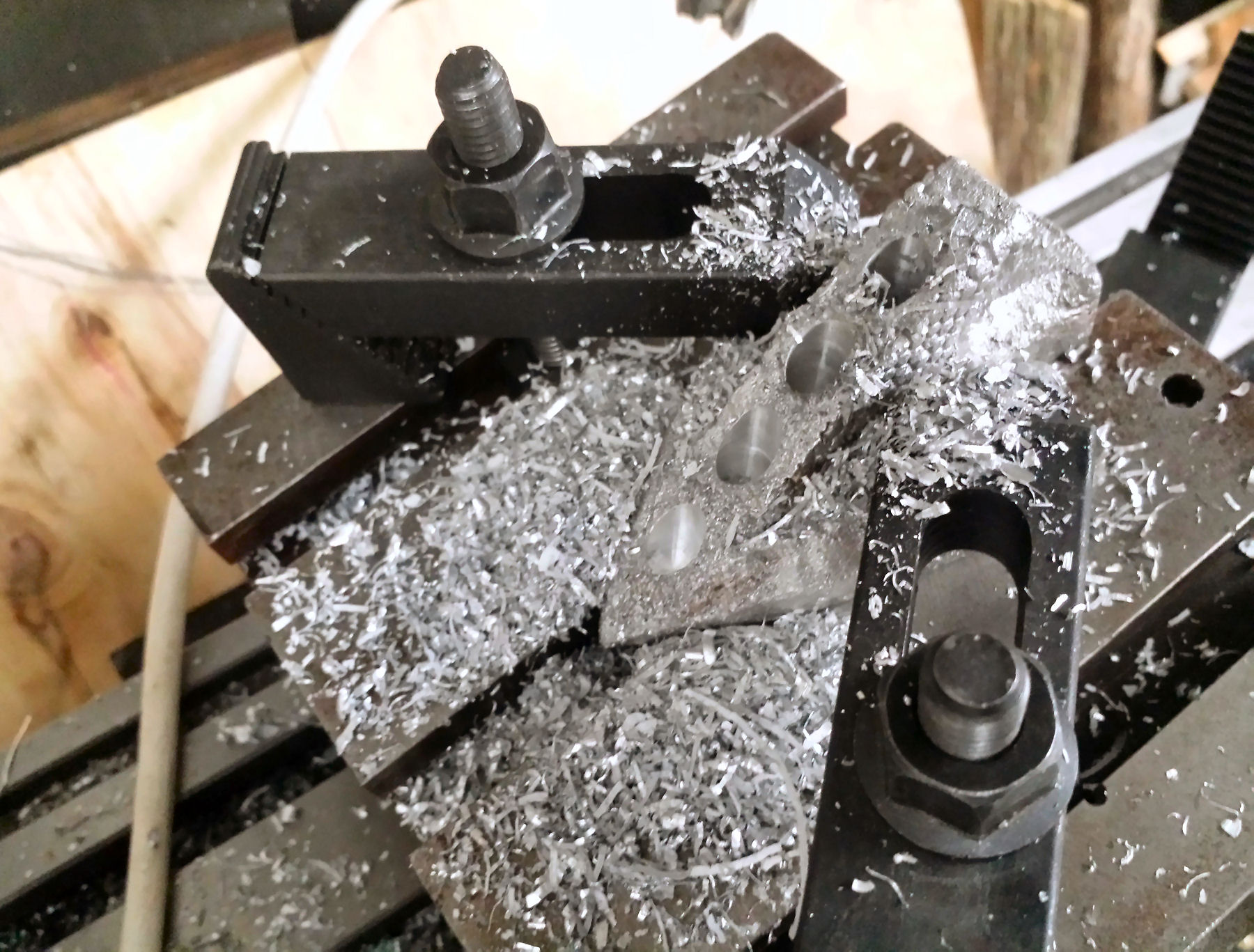
The main thermal conductivity, tensile toughness, yield stamina, and elongation vary. Among the above alloys, A356 has the greatest thermal conductivity, and A380 and ADC12 have the lowest.
Getting My Alcast Company To Work
In precision spreading, 6063 is well-suited for applications where complex geometries and top notch surface area finishes are paramount. Instances include telecommunication units, where the alloy's remarkable formability enables smooth and cosmetically pleasing layouts while preserving structural stability. Similarly, in the Illumination Solutions market, precision-cast 6063 parts create elegant and efficient lighting fixtures that call for intricate shapes and excellent thermal performance.
The A360 exhibits remarkable prolongation, making it suitable for complicated and thin-walled elements. In accuracy casting applications, A360 is appropriate for industries such as Consumer Electronic Devices, Telecommunication, and Power Tools.
Fascination About Alcast Company
Its distinct residential properties make A360 a useful choice for accuracy casting site here in these sectors, improving product durability and top quality. Aluminum alloy 380, or A380, is an extensively used casting alloy with a number of distinctive qualities. It offers excellent castability, making it an ideal choice for accuracy casting. A380 shows good fluidness when molten, ensuring intricate and comprehensive mold and mildews are properly duplicated.
In accuracy casting, aluminum 413 shines in the Customer Electronic Devices and Power Devices markets. This alloy's exceptional rust resistance makes it an exceptional selection for outside applications, ensuring resilient, sturdy products in the stated markets.
The 20-Second Trick For Alcast Company
As soon as you have determined that the light weight aluminum die casting process is ideal for your job, a critical following step is choosing the most ideal alloy. The aluminum alloy you choose will considerably affect both the spreading procedure and the buildings of the end product. Because of this, you must make your decision meticulously and take an enlightened technique.
Determining one of the most appropriate light weight aluminum alloy for your application will certainly indicate evaluating a wide variety of qualities. These comparative alloy qualities follow the North American Pass Away Casting Organization's standards, and we have actually separated them right into 2 categories. The initial group addresses alloy characteristics that affect the manufacturing process. The 2nd covers attributes affecting the buildings of the end product.
Facts About Alcast Company Uncovered
The alloy you pick for die spreading directly influences several facets of the spreading process, like how very easy the alloy is to deal with and if it is susceptible to casting flaws. Hot cracking, likewise known as solidification cracking, is a normal die casting defect for light weight aluminum alloys that can result in internal or surface-level splits or cracks.
Particular light weight aluminum alloys are much more vulnerable to warm fracturing than others, and your selection needs to consider this. Another typical issue found in the die casting of aluminum is die soldering, which is when the actors stays with the die walls and makes ejection difficult. It can damage both the actors and the die, so you need to search for alloys with high anti-soldering residential or commercial properties.
Deterioration resistance, which is currently a significant characteristic of aluminum, can differ considerably from alloy to alloy and is a vital characteristic to take into consideration depending upon the ecological conditions your product will certainly be subjected to (Foundry). Use resistance is another building generally looked for in light weight aluminum items and can differentiate some alloys
Report this page